スマートフォンや乗り物など、生活に欠かせないもののほとんどに、半導体という小さな部品が組み込まれています。半導体をつくるうえで欠かせない、多くの半導体製造装置が岡山にあるタツモ株式会社で開発・設計・製造されています。世界に誇る半導体製造装置技術を有するタツモ株式会社の搬送事業部で働く飛田さんに、大学生の磯野さんがお話を伺いました。
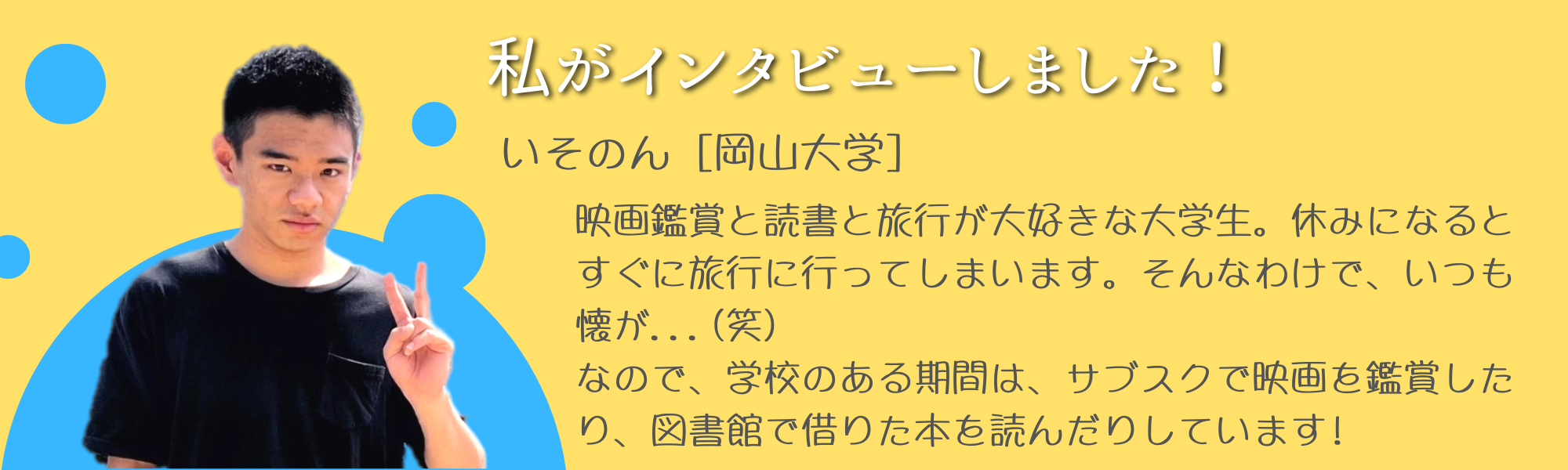
目次
企業活動を深掘りしてみる
半導体製造装置の技術で世界トップレベル
――御社の事業について教えてください。
――半導体ってよく聞くのですが、具体的にはどんなものですか?
技術の進化とともに、半導体そのものの性能も向上しています。つまり、できることが増えているんです。たとえば携帯電話だと、一昔前は電話をかけることとテキストを送ることしかできなかったけれど、今は動画など大容量のデータを高速で送ることができるようになっていますね。インターネットの利用も、電話の回線を有線で利用しなければ接続できませんでしたが、今はさまざまな場所でWi-Fiに接続して無線で利用することができます。
現代社会ではいたるところで半導体が欠かせません。
――半導体はどのように作られているのですか?
半導体は、直径30㎝、厚さ1mmのシリコンウェハーをシリコンの材料から切り出す工程に始まり、チップになるまで、500もの工程があるといわれています。タツモでは、洗浄する装置、薬液を0.1mmよりも薄く塗る装置、ウエハを薄くするためにガラスと張り合わせる装置など、工程ごとの装置を開発・設計・製造しています。 半導体一つひとつは小さいため、半導体をつくる装置はナノメートル単位での作業をおこないます。装置の動作が少しでもズレると、何千、何万もの半導体が不良品になってしまう可能性があるため、装置をいかに正確に、効率的に稼働させられるかがとても重要なんです。半導体製造装置の製造は、誰でもできることではなく高度な技術が必要。タツモの半導体製造装置は、その技術を評価していただき、世界で長年高いシェアを誇っています。
半導体工場は、そういった皆さんがイメージする工場とは少し異なります。半導体はたくさんの工程をへて、1~2ヶ月ほどかけて完成するのですが、その工程ごとに異なる装置が稼働しています。ひとつのラインに長いベルトコンベアが敷かれていないかわりに、工程ごとに装置が並んでいます。その装置の中ではタツモのロボットをはじめとするさまざまなロボットや搬送用の機械が活躍しています。
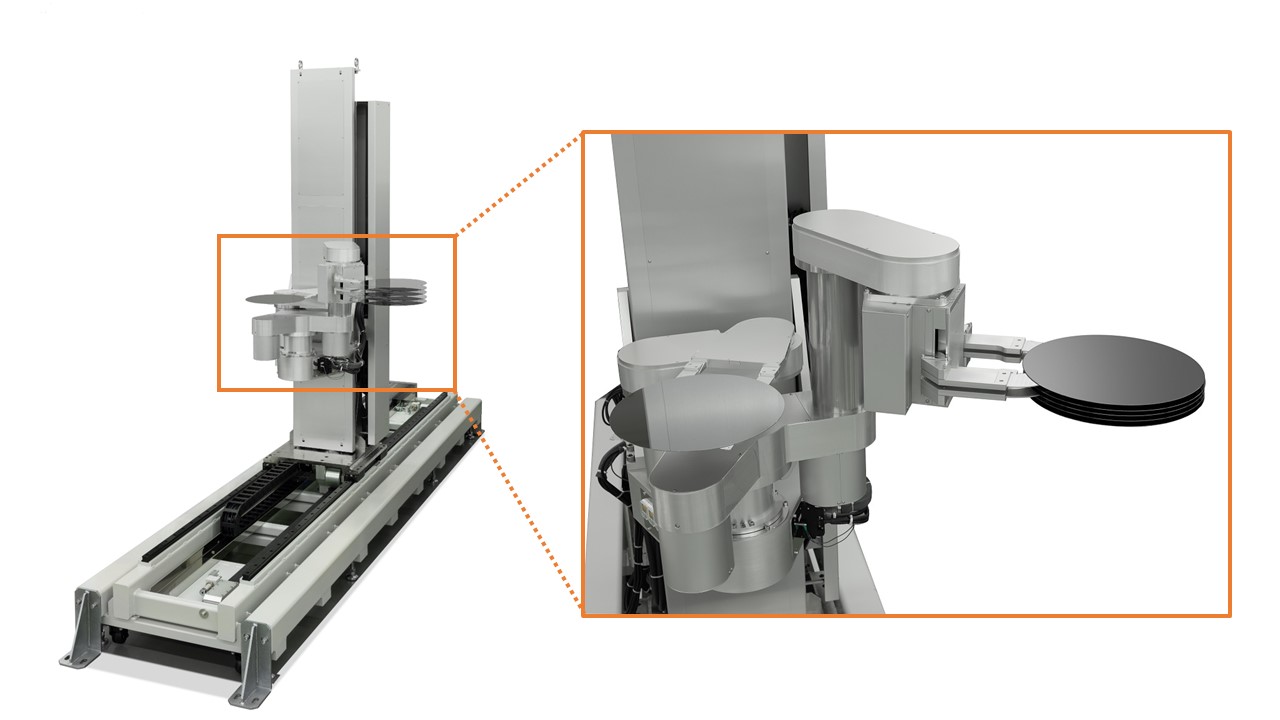
シリコンウェハを搬送するロボット。半導体工場は、昼夜を問わず24時間稼働し続けるため、高い信頼性が要求される。また、半導体は空気中に漂う細かいチリ(微粒子)の混入を嫌うため、ロボットもごみや埃を出さないものが求められる。
コーティング技術を液晶ディスプレイにも活かす
――すごいですね!半導体製造装置と液晶ディスプレイのコーティングは、どのように関係しているんですか?
――そうだったんですね!
赤にしたい場合は、赤の窓だけに光を当てます。ピンクにしたい場合は、光は異なる色が重なるほど白くなるという性質を利用して、色の割合を調節するといった具合です。赤の層、青の層、緑の層で、それぞれ厚みが異なるとダメで、赤の層が厚いと赤色の強いテレビになってしまう。均一に塗ることがとても重要なんです。タツモが持つ、塗料などを均一な厚さにする技術や、ナノレベルで塗ることができる技術は世界トップレベルとして、評価していただいています。
オーダーメイドで競合他社と差別化
――御社ではオーダーメイドで製品を開発していると伺いました。なぜ量産するのではなく、オーダーメイドで生産しているのでしょうか?
飛田さんの「働く」を深掘りしてみる
働く人の姿を実際に見て「入社したい」と思った
――飛田さんが入社されたきっかけを教えてください。
今は、2019年12月の岡山市の本社移転時より岡山市の本社に勤務しています。
会社見学で、工場で装置の組み立ての様子や、設計する人の仕事など、さまざまなところを見ることができました。タツモで生き生きと働くひとたちをみて、自分もこのような場所で働きたいなと思って、応募しました。
要望にこたえるため緻密に連携
――飛田さんは、今どのような仕事を担当されているのですか?
――先ほどオーダーメイドのお話がありましたが、どういう流れで要望を実現するのでしょうか?
相手に敬意を持って一生懸命仕事をする
――入社されてから自分の成長を感じた場面はありますか?
――仕事の取り組み方が変わったのですか?
お客様が困っていることに対して、できる限りのことを精一杯取り組んで、解決する。誰かと仕事をするときに、自分が敬意を持って接すると、相手も敬意を持って返してくれることがわかってから、相手のことを思って一層一生懸命に仕事をするようになりました。そういう仕事をしてお客様が喜んでくれたら「やってよかった」と感じます。
そんなときに、お客様に「日本から来て心細いだろうけど、よく頑張ってくれている」と評価していただいたんです。いろいろ気を使ってくれたりして。「ありがたい。ちゃんと恩に報いないといけない」と思って、できるだけ良いものを作ろうと頑張りました。
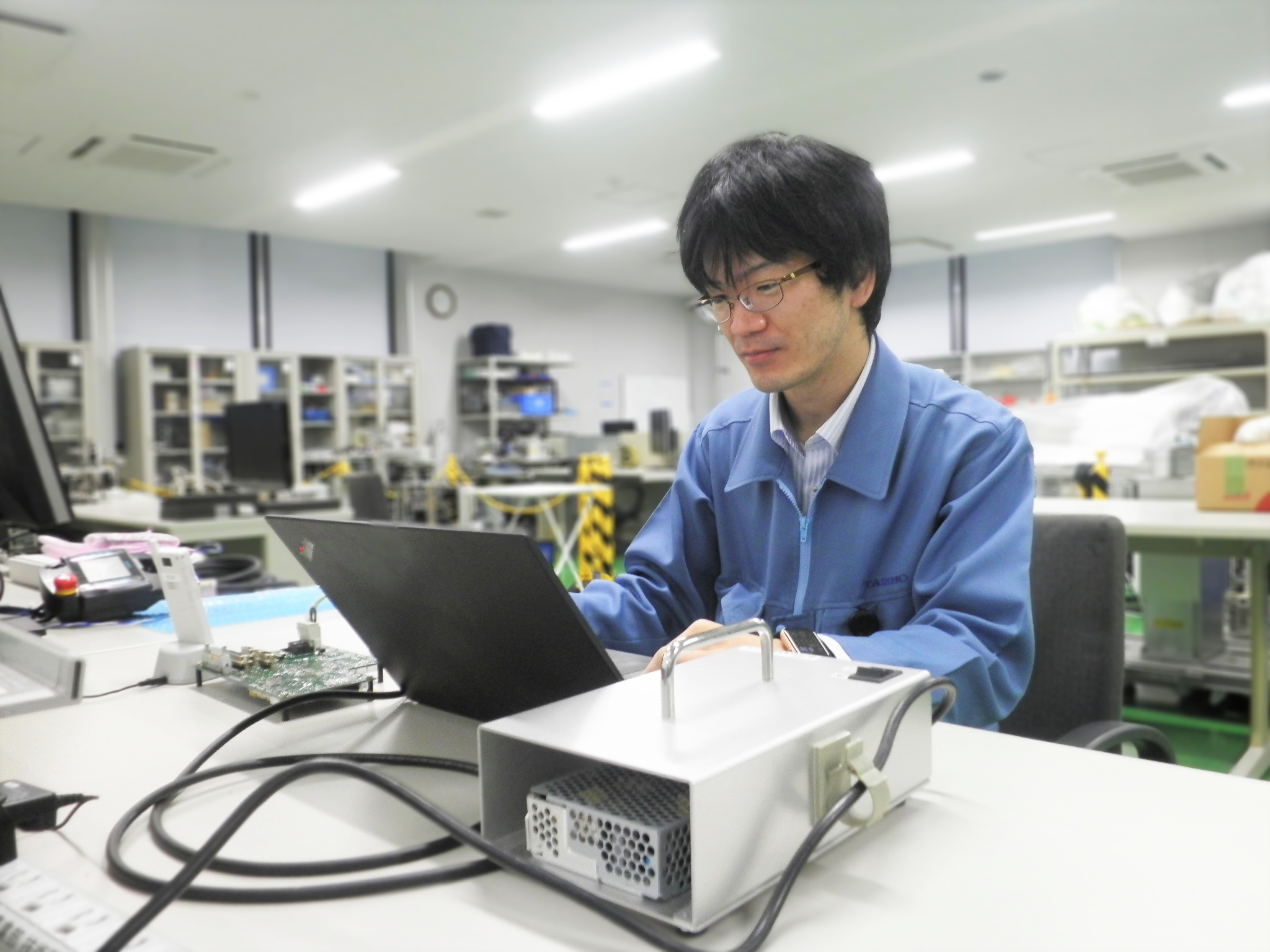
目指したい未来について聞いてみる
新しい価値を提供する商品と人を増やす
――経営理念でもある「挑戦」について伺います。今後、会社として挑戦していくことがあれば教えてください。
具体的には、どんどん新しい商品をつくっていくことと、会社全体としては体制が大きく変わって人材育成も進んでいくことですね。
半導体業界でお客様の役に立つ商品をたくさん開発でき、半導体製造で培った技術を液晶ディスプレイのコーティングに応用できたように、別の業界でも役に立つものを何かつくることができるかもしれない。
新しい価値を生み出すためには、新しい価値を生み出せる人材になることも大切だと考えています。
技術を応用するための水平思考
――飛田さんが挑戦について意識していることはありますか?
ある技術がその業界で使われることが当たり前になったとき、「技術が枯れた」という言い方をします。けれど、別の業界でその技術が新しい技術として受け入れられるケースもあります。
スマートフォンが登場する前は、タッチパネルではない携帯電話が一般的でした。スマートフォンが出てきてタッチパネルで操作できることに感動した人は多いと思いますが、タッチパネル自体は銀行のATMなど、スマートフォンが登場する以前から存在していた技術です。
そんなふうに、時代の変化に柔軟に合わせていく。1つの技術を応用して新しい価値や商品をどんどん生み出していきたいです。
(編集:金城 奈々恵)